Intelligence in preventive fire protection - How do I digitalise a water tap?
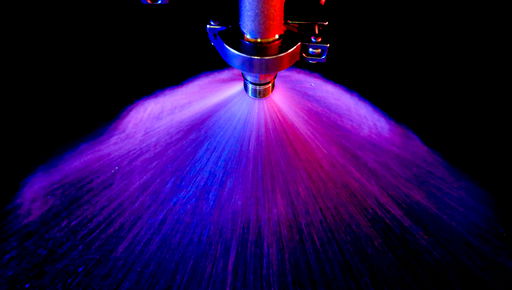
Previous extinguishing components in spark extinguishing systems are quite simple. They can be switched on after an ignition source has been detected and switched off again when the extinguishing has been successful. The monitoring of the extinguishing process also provides little information other than the statement that water is flowing or not.
Classic spark extinguishing systems equipped with established extinguishing technology do their job reliably. Nevertheless, it is difficult to make a statement about the quality of the water flow or about the general conditions of the water flow. You have to be on site and personally monitor these processes with a lot of time on your hands.
Development protects lives and values
In Alfeld, Lower Saxony, where Fagus-GreCon is at home, systems for preventive fire protection have been developed for a good 50 years. In keeping with the company's credos "Innovation is our tradition" and "Protecting lives and values", the research and development department of the fire protection business unit takes care of creating new and improved products from new customer requirements, guidelines and technologies.
"Protecting lives and values" also means improving good products and making it easier for users to operate our solutions. From our experience, we have found that it is not only important to ensure the detection of ignition sources that occur in order to prevent fires before they start. The quality of extinguishing and the monitoring of relevant performance parameters are also of great importance, for example to be able to carry out any necessary system maintenance in good time. This includes the question of whether water is flowing at all. Is it flowing fast enough? Is the amount of water sufficient during the extinguishing process?
If the extinguishing system is not activated, it must be ensured that water is present and that no water escapes from the extinguishing system. The latter is particularly relevant for operators who produce food or other products that are sensitive to moisture. The extinguishing system must be tight, especially in such systems. No water must be allowed to escape.
In order to be able to answer these questions smartly, our development team had to face the challenge of digitising the simple water tap, which until now could only be switched on and off. The end result of the development process is the new GreCon Intelligent Extinguishing Module IEM, which is used in our spark extinguishing systems.
The new extinguishing system precisely enables the necessary high-precision monitoring of the extinguishing process, detects blockages, measures the flow pressure and detects premature wear of nozzles and valves. Leakages are also detected and automatically reported.
Continuous review supplements maintenance intervals
Critical equipment such as spark extinguishing systems must be checked and maintained at set intervals to ensure reliable operation. With the new extinguishing system, blockages and wear can be detected at an early stage in order to maintain the best possible availability of the spark extinguishing system.
In addition, maintenance intervals can be defined individually in the future based on wear data determined by the intelligent extinguishing system. These dynamic maintenance intervals resulting from the actual wear data not only extend the maintenance intervals themselves, but also increase the safe service life of the components monitored in this way.
In search of the new tap
The decision on what a new extinguisher should look like for a mature, established solution for extinguishing sparks and other ignition sources is not made by a stroke of the pen. At the beginning of the development process, in the requirements phase, various options were used to write the right features of the new extinguishing generation into the development backlog.
In addition to the new features that were incorporated based on experience in the development, installation and maintenance of spark extinguishing systems, the GreCon developers used various methods to determine and evaluate customer and technical requirements.
One method that was used is Quality Function Deployment (QFD). It separates the pure customer requirement, which describes what is needed, from the required technical implementation. All results of the QFD process are visualised in the so-called House of Quality. Based on these results, a prioritised list of product features that ultimately need to be developed can finally be written.
One product feature that was integrated into the new quencher via this method is the integrated heating cartridge, which acts directly in the metal and can thus keep the quench at temperature right up to the nozzle. This prevents freezing.
For the development process, the QFD method is a helpful tool to organise and prioritise requirements. In addition, the process itself is a communication tool to bring on board all those who have to work with the product after completion, from sales, who plan systems for the customer, to customer service.
Important impulses and insights have also flowed from the implementation of other products into the realisation of the extinguishing. The development of the new DLD 1/9 spark detector was based on the results of cooperation with several universities. These findings are also reflected in the development of the new extinguisher.
Next Steps
Constantly changing requirements for spark extinguishing systems are also based on changes in the customer process and the use of new manufacturing materials. The ever-increasing desire not only to collect data but also to implement Big Data strategies also has an impact. The result is necessary optimisations of spark extinguishing centres as data collection and evaluation nodes within the spark extinguishing system. With the information gained from the spark extinguishing system about spark detectors and extinguishing, risks must be further minimised and production processes optimised.
This is already happening with some customers who can make new decisions based on the data from the spark extinguishing system. Events such as the number of sparks detected are important information that, if interpreted correctly, enables new risks to be identified at an early stage and the status of the existing process to be better assessed. This is an example of how a trend can be used to derive actions that lead directly to improvements.
Conclusion
The more and better data the spark extinguishing system provides to an automated evaluation centre, the further it integrates itself into the production process. In this way, the spark extinguishing system becomes more and more part of the production plant. They become part of Big Data strategies and help to drive customer processes better.
Like the smart spark detector DLD 1/9, intelligent extinguishing contributes to the digitalisation of established processes. As the organisation of work changes with digitalisation, the interaction of the end user with the spark extinguishing system also changes. Fewer staff at control stations and location-independent work requires being able to access data everywhere, so as not to have to run to the control centre or the control station. This increased information flow also plays an increasingly important role in the information security of the systems and data.